Border inspection of imported used vehicles
Correct as at 26th April 2024. It may be superseded at any time.
News and updates
-
24 April 2024
Inspection news issue 15 out now
-
01 April 2024
1 April 2024 VIRM amendments in effect
-
27 March 2024
30 April 2024 VIRM amendments available to preview
-
27 February 2024
Registration plate amendment now delayed
-
13 February 2024
Industry alert issued: Risk of cracks in perforated chassis rails
-
07 February 2024
Safety alert issued: Heavy full trailer drawbar hinge pin failures
Introduction
1 Purpose and Scope
The NZ Transport Agency Waka Kotahi (NZTA) has prepared this manual to assist vehicle inspectors and inspecting organisations in achieving correct and consistent standards for the border inspection of imported used vehicles entering New Zealand.
The purpose of the manual is to explain the conditions of appointment and the requirements for the border inspection of imported used vehicles that are entering New Zealand.
This manual applies to the border inspection of imported used vehicles. The types of vehicles that need to be inspected are listed in section 3.2.
Amendments to this manual will be issued from time to time as inspection requirements change and improvements are made. Details of amendments are available from the Amendments tab on the horizontal menu. Suggestions for improvement should be made using the feedback button found on every page.
2 Contacts
The following are contact details for the NZ Transport Agency:
National Office
Vehicles
Operational Standards and Guidelines
50 Victoria Street
Private Bag 6995
Wellington 6141
Tel: 04 894 5400
Fax: 04 894 5011
NZTA Border Inspections (BIS Data Entry)
Private Bag 11777
Palmerston North 4442
Tel: 0800 804 580 (option 4)
From outside New Zealand: +64 6 953 6200
Fax: 06 953 6282
Email: info@nzta.govt.nz
3 The border inspection process
In order to inspect a vehicle at the border the vehicle inspector and inspecting organisation must take the following steps:
1. Know the vehicle inspector’s and inspecting organisation’s responsibilities. Part 3.1 of this section lists the legal responsibilities. The vehicle inspector and inspecting organisation must read and understand them.
2. Establish whether the vehicle requires a border inspection. Part 3.2 of this section explains how to determine if a vehicle requires a border inspection.
3. Establish whether the vehicle with damage needs to be flagged. Part 3.4 of this section explains how to determine if a vehicle needs to be flagged with damage.
4. Complete the required inspection documentation. Part 3.5 of this section explains the requirements for handling of photographs and completing check sheets.
5. Record the inspection outcome. Part 3.6 of this section explains how to notify the Transport Agency of the information collected at the Border Inspection.
6. Collect fees. Part 3.9 of this section lists the requirements for the inspecting organisation when charging and collecting fees.
3.1 General duties and responsibilities
Applicable legislation: Land Transport Rule: Vehicle Standards Compliance 2002 (Rule 35001/1) (‘the Rule’)
3.1.1 Vehicle inspectors and inspecting organisations (definitions in the Rule)
Vehicle inspector means an individual appointed by the Transport Agency under section 2.2(1) of the Rule to carry out inspection activities in accordance with requirements and conditions imposed by the Transport Agency.
Inspecting organisation means a person or organisation appointed by the Transport Agency under section 2.2(1) of the Rule who is responsible for inspection outcomes.
In this manual, a vehicle inspector or inspecting organisation is appointed for the purpose of border inspection of imported used vehicles, unless stated otherwise.
To avoid doubt, any reference to a certifier in any legislation, notice of appointment, or any other relevant document is a reference to a vehicle inspector or inspecting organisation (as applicable) appointed by the Transport Agency under the Rule.
3.1.2 Document retention (section 2.3(4) of the Rule)
A vehicle inspector or inspecting organisation must:
a) keep, for at least five years, the original of any documents that have been collected in the inspection process
3.1.3 Advise incorrect inspection and/or vehicle defects (section 2.3(4) of the Rule)
A vehicle inspector or inspecting organisation must:
a) advise the Transport Agency as soon as practicable if there is a reason to believe that the inspection of a vehicle has been carried out incorrectly
3.1.4 Delegation (section 2.4(1) of the Rule)
A vehicle inspector or inspecting organisation may not delegate any function or power to carry out inspection activities for which they were appointed, except under conditions specified by the Transport Agency in writing.
The only tasks that may be delegated to non-approved staff are administrative processes such as recording vehicle attributes or removing and replacing components to enable the inspection process to be carried out.
3.2 Establishing whether a vehicle is required to have a border inspection
The inspection organisation will ensure that all used vehicles imported into New Zealand for the purpose of registration are inspected at the border before they are released to the owner/importer. The only exceptions are:
a) New vehicles
b) Vehicles imported by a person who is approved by the Transport Agency in accordance with the relevant Regulation, or Rule as a certifier for vehicles of that make
c) Overseas visitors' vehicles (imported temporarily with overseas registration)
d) Vehicles returning to New Zealand that have current New Zealand registration
e) Vehicles that the owner declares are not going to be registered in New Zealand
f) Vehicles that are described in section 6.1 of the Land Transport Rule: Vehicle Standards Compliance 2002, that is:
- vehicles of class AB, TA or TB
- armoured vehicles used exclusively as equipment of the New Zealand Defence Force
- traction engines
- mechanically propelled rollers
- tractors (other than agricultural tractors) and machines, including trailers, for use solely in non-agricultural land management or roading operations, whether for traction or otherwise
- agricultural motor vehicles
- vehicles registered for use on a road in a country other than New Zealand that are not going to be in New Zealand for a continuous period of more than 18 months (see VIRM: Entry certification Technical bulletin 5 – Inspection requirements for temporary vehicle imports)
- vehicles listed below:
a) pedestrian-controlled goods service vehicles
b) vehicles propelled and supported solely by self-laying tracks
c) vehicles used on roads only in road construction zones in accordance with notices declaring those zones
d) vehicles that are used on a road only when crossing or proceeding along a section of the road where the vehicles have been authorised to operate by an authorisation of a road-controlling authority that requires:
i. a written agreement by the vehicle’s operator or the person for whom the vehicle is being operated, to construct, reconstruct, maintain, or restore to the satisfaction of the road-controlling authority all or part of the road used by the vehicle, and
ii. the erection and maintenance of warning devices, signs or control devices as required by the road-controlling authority and the director, and
iii. where the use of the road does not consist solely of the direct crossing of the road, the prior approval of the NZ Transport Agency
e) all-terrain vehicles that are used on a public highway
f) motor vehicles exclusively designed and used on a road for driving, carrying or propelling any of the following, which must be permanently attached to the vehicle:
i. aerodrome runway sweepers
ii. electrical substations
iii. filters for transformer oil
iv. log haulers that are stationary when hauling logs
v. aero engine test benches
g) tractors owned by a local authority and used exclusively for the construction, maintenance or mowing of stopbanks and the banks of rivers, streams, drains, canals or other watercourses
h) mobile or movable huts, galleys or similar motor vehicles that are used on a road solely in connection with the construction or maintenance of roads
i) tractors used exclusively for shunting railway rolling stock
j) traction engines
k) forklifts
l) aerodrome crash fire tenders that are used on a road only in emergencies
m) trailers while being drawn by a motor vehicle specified in (n) to (s) of this schedule
n) motor vehicles, used exclusively in connection with the embarking and disembarking of ships’ passengers or for loading and unloading ships’ mail, cargo, and passengers’ baggage, and used on a public highway only when proceeding unladen from one wharf to another wharf or from its usual place of storage to a wharf and returning to that place of storage
o) motor vehicles designed exclusively or principally as part of the armament of the New Zealand Defence Force
p) cable jinkers
q) front-end loaders
r) log skidders
s) tractor cranes
t) rough-terrain cranes
u) mobile crushing and screening plane machines, which are mounted on trailers
v) motor graders
w) motor scrapers
x) trailer scrapers
y) plant for servicing oil-filled cables
z) post debarkers
aa) saw bench apparatus
bb) forestry chippers
cc) tree feller bunchers
dd) trench diggers and excavators
ee) vehicles that are always used unladen on the road and that are designed exclusively for carrying earth or other bulk materials
ff) mobile concrete mixers that are mounted on tractors
gg) a vehicle that is similar in design, construction or purpose to a vehicle listed above that cannot be categorised by vehicle class.
3.3 Vehicle inspection
3.3.1 Inspecting a vehicle at the border (section 4.2 of the Rule)
The inspection of a vehicle at the border must be carried out in accordance with requirements and conditions imposed by the Transport Agency.
The vehicle inspection must be completed before a vehicle can be released from a customs-controlled area to the vehicle owner/importer. If the border inspection organisation wishes to use an alternative inspection procedure, they must contact the Transport Agency for prior approval.
From 21 May 2018 the vehicle inspection must include a check to see if the vehicle is on one of the lists of vehicles that must be damage flagged with notes recorded stating ‘Open Airbag Recall’. See Technical bulletin 1: Takata airbag recall for how to do this.
3.3.2 Information to be recorded at the border inspection (section 4.3 of the Rule)
A vehicle inspector or inspecting organisation must record and provide to the Transport Agency, or to other persons specified by the Transport Agency, the following information about a vehicle inspected.
a) its make, model, and vehicle identification number or chassis number
b) the name and address of its importer
c) its odometer reading
d) any obvious defects or damage identified in the inspection
e) left-hand drive
f) border inspection date
g) ship name
h) country of export and port of arrival
i) inspection site and inspector ID.
Note 1
When recording the VIN/’other VIN’ No. take the number from the manufacturer’s stamp (into bodywork/chassis of the vehicle) or the manufacturer’s ID plate.
Note 2
If it is not possible to record an odometer reading, write zeros in the odometer field on the check sheet.
Note 3
When checking the condition of the vehicle the following items shall be inspected but not necessarily in the order shown:
- Engine compartment
- Right side
- Luggage cargo compartment
- Left side
- Under body or chassis frame
- Passenger compartment.
Note 4
The vehicle inspector or inspecting organisation may refuse to inspect a vehicle because the vehicle is presented in such a condition that inspection is unreasonably difficult or cannot be completed (eg components covered in dirt, components missing etc), or
Note 5
Where the vehicle inspector requires further information in order to carry out an inspection, the inspector must reject the vehicle until the information has been obtained.
Note 6
The inspector ID is the person’s initials, followed by a sequential number which identifies the inspector.
Note 7
Used vehicles (imported from Japan) that have had the vehicle identifier partially or totally removed cannot be border inspected for the NZTA unless the vehicle has been re-identified by the Japanese Ministry of Land, Infrastructure and Transport (MLIT) and issued with an authentic Export Certificate that list the new identifiers.
3.4 Establishing whether a vehicle with damage needs to be flagged
To establish whether a vehicle with damage needs to be flagged:
Refer to Reference material 1 for guidelines for the detection of reportable damage on imported used vehicles.
3.5 Checksheets, photographs and affixing inspection sticker
All inspections shall be recorded on an electronic or paper-based checksheet (see Reference material 7a or Reference material 7b) that has the prescribed information and signed by the inspector. All locations where the inspector observes indications of structural damage or deterioration shall be recorded and photographed. In most cases two photographs (usually a wide shot showing the whole front, rear, or side of vehicle and under-body shot) of the damaged/deteriorated area and a close up shot is required. One photo is OK if the damaged/deteriorated area can be clearly identified and the extent of the damage is obvious. The inspector can use their discretion to determine how many photos are required. The maximum number of photographs required for any vehicle would be four.
If requested, a copy of the checksheet must be supplied to the vehicle owner.
At the completion of the inspection, affix an ‘Border Inspected’ sticker to the wiper arm on the driver’s side of the vehicle.
Note 8
For motorcycles, place the inspection sticker onto the headlamp glass/lens.
3.6 Notification to the Transport Agency of the information collected at the border inspection
3.6.1 When the inspection has been completed the inspection organisation will notify the NZTA’s database.
See Reference material 2 for the data transfer process.
3.6.2 On a vehicle where any damage or deterioration has been detected, the inspector will be required to attach a label (NZTA notice to the Importer).
See Reference material 3 for a sample of the label. The label must be placed on the inside of the windscreen in the bottom right hand corner (when sighted from the driver’s seating position).
Note 9
For water-damaged vehicles, mark the vehicle with a large "W".
3.7 Vehicles presented for a border inspection after being released from customs
If a vehicle is presented for a border inspection after it has been released from customs there are additional requirements. Refer Reference material 9 for the additional inspection requirements.
3.8 Disputes
If an importer disputes the decision to report or flag damage they may present the vehicle to an approved Transport Agency entry inspector or repair certifier for re-consideration.
If an importer or owner dispute arises: report the incident to Transport Agency immediately.
3.9 Collecting fees
NZTA has a set regulatory fee (Section [8A of the Land Transport (Certification and Other Fees) Regulations 2014) for the border inspection process. The inspecting organisation will collect the $6.33 (incl. GST) fee as part of their invoice to the customer for the full inspection service.
For inspections carried out offshore, the border inspection fee will not include GST and will be $5.50 per vehicle.
The inspection organisation will be solely responsible for ensuring that the customer is charged the correct Transport Agency border inspection fee and that the fee is paid to the NZTA as specified in the flowchart below:
Page amended 16 May 2018 (see amendment details)
4 Complaints
Encourage customers to direct any complaints to the inspecting organisation in the first instance.
To ensure that all written complaints are investigated, the inspecting organisation must maintain an effective complaints management process and provide the following:
a) a clear and concise statement that recognises the positive value of complaints
b) clear and concise instructions to all customers on how to register a complaint. This can be accomplished in several ways, for example:
- a clear notice visibly displayed on the workplace wall
- a clear statement on any receipt or invoice issued
- a clear statement on the inspecting organisation’s checksheet
c) a straightforward explanation of the expected standards for resolution and the customer’s right to appeal to the NZTA if they are dissatisfied with the proposed resolution
d) documentation of complaint investigations, prepared in accordance with the Border inspection organisation’s (BIOs) manual so that details of the investigation can be readily checked
e) acknowledgment in writing of all written complaints within three working days, with the investigation completed and a resolution proposed to the complainant within 20 working days, of the complaint being made
f) a record of all complaints, both verbal and written, recorded in accordance with the BIOs manual
g) directions, for any customer who wishes to make a complaint or appeal a decision made by an inspecting organisation, to use the NZTA free phone 0800 699 000.
5 Inspection premises and equipment
5.1 The inspector must carry out the border inspection in an inspection area that:
a) enables a safe and thorough inspection
b) is situated within a structure that has a roof and sides, and:
i. is of sufficient dimensions to enable the efficient and thorough inspection of any vehicle
ii. is on ground that is constructed of a material that will remain firm in all weather conditions
iii. is on ground that is even and level (the ground will be considered level when it can be demonstrated that a vehicle will remain stationary with all brakes released)
iv. is sufficiently clear of structural and equipment intrusions (other than those necessary for the inspection process) to enable the efficient and thorough inspection of any vehicle.
v. is provided with sufficient lighting to enable good visibility of the vehicle being inspected and the equipment used in the inspection process.
Note 1
The upper body and internal inspection can be carried out in an open area if the weather condition and natural light is good. When the weather is bad (rain and snow) and the natural lighting is poor the upper body and internal inspections must be carried out in the inspection area detailed in section 5.1 (above).
5.2 The inspection area must provide the following equipment for the inspector to use as required:
a) an inspection hoist, pit or ramp that enables the efficient and thorough close visual inspection of the complete vehicle underbody
b) an industrial-quality, hand-held inspection lamp (500 lux minimum)
c) a digital camera which is capable of taking photos that meet the following specifications:
- 640 x 480 pixels in size
- RGB, 24 bits per pixel
- Minimum DPI of 72, maximum of 180.
5.3 Compliance with statutory requirements
It is the inspection organisation’s responsibility to ensure that the premises and equipment comply with: occupational safety and health requirements and any other relevant acts, regulations and local bylaws.
5.4 Other requirements and considerations
The computer equipment, and document storage must be located and operated from a location where the public does not have access when staff are not present.
Inspection area lighting should conform to New Zealand standard code of practice for interior lighting design (NZS 6703:1984), or subsequent amendments. The code of practice establishes performance requirements for specific workplace lighting.
6 Appointments
Vehicle inspectors
To allow the inspecting organisation(s) to ensure continuity of service provision, vehicle inspectors will not be appointed by the NZTA. The approved inspection organisations(s) will have permission to delegate employees as vehicle inspectors if they meet and maintain the minimum NZTA vehicle inspector requirements. It will be a responsibility of the inspection organisation to track, monitor, record, audit and train the vehicle inspectors.
The vehicle inspector must:
a) demonstrate a comprehensive knowledge of the requirements in the VIRM: Border inspection of imported used vehicles, sufficient to inspect a vehicle at the border
b) have attended an approved two-day course in structural integrity and energy management, and achieve the required pass standard
c) be a fit and proper person (section 2.6 of the Rule). Refer to the NZTA’s fit and proper person guidelines for inspection organisations and vehicle inspectors
d) be physically capable of carrying out the border inspection process
e) be able to pass a basic eyesight test.
7 Definitions and abbreviations
NZTA | means the NZ Transport Agency |
Make | in relation to a motor vehicle, means the name given for market identification to a group or groups of motor vehicles by a company or organisation which owns that name. |
New motor vehicle | In relation to a vehicle, means a vehicle that: a) has not been registered and operated in New Zealand or any other country, and |
Structural damage | Includes any of the following:
|
Used motor vehicle | means a vehicle that is not a new vehicle. |
Page amended 3 October 2023 (see amendment details)
Technical bulletins
1 Takata alpha airbag recall
The compulsory Takata alpha airbag inflator recall order 2018 becomes effective from 31 May 2018. From the effective date Takata alpha airbag inflators become a prohibited import as well as being prohibited for sale in trade.
The purpose of this technical bulletin is to outline the process to identify vehicles subject to the mandatory Takata Alpha type airbag recall and how to deal with them.
The process outlined below are the steps BIOs can take to assure they act with due diligence, best endeavours, and based upon the best information available.
Border Inspection Organisations
The Border Inspection Organisations, specifically Automotive Technologies Limited, ATJ, JEVIC, Independent Verification Systems (IVS), and NZ Biosecurity Services, as per the requirements of the Boarder Inspection VIRM, will provide data to the Transport Agency regarding open safety recalls on vehicles they inspect subject to the prerequisites below.
All reasonable efforts outlined in this process will be made to assure they provide the most accurate information. All responsibility for importing any vehicle remains with the importer.
The process
From 21 May 2018, Border Inspection Organisations must check if vehicles they inspect (that are fitted with airbags) are on the Takata airbag recall lists from the various source countries.
Recalled Takata Alpha airbag vehicles from Japan
In Japan, vehicles subject to this recall are listed under the Japanese Ministry of Land, Infrastructure, Transport and Tourism (MLIT) definition ‘Vehicle of concern’. The Transport Agency is using this list to populate our website at www.vehiclerecallsafety.nzta.govt.nz/takata/importers. This website is the Transport Agency definitive list of vehicles in Japan that require rectification due to the fitment of Takata Airbags that are under recall.
For vehicles from Japan a further search can be conducted on the MLIT web site at the following address to check whether the recall has been closed in Japan, if it has no action needs to be taken: https://www.jaspa.or.jp/portals/recallsearch/index
Recalled Takata Alpha airbag vehicles from other countries
Vehicles from countries other than Japan will have to be checked against official sites in those countries that are covering the Takata recalls. These include, but are not limited to:
- USA
https://www.nhtsa.gov/recalls - Australia
https://www.productsafety.gov.au/recalls/compulsory-takata-airbag-recall/takata-airbag-recalls-list - UK
https://www.dft.gov.uk/vosa/apps/recalls/default.asp - There may be appropriate lists in other jurisdictions.
It is important to understand that this is not a new requirement it is just enforcing the existing requirement that recalls are to be closed prior to a vehicle being imported into New Zealand.
If the vehicle is on one of the lists and conclusive evidence from the manufacturer or jurisdictional authority that the airbag recall has been completed is not available, the vehicles will be damage flagged with notes recorded stating ‘Open Airbag Recall’.
Vehicle makes to check
Other than for left-hand drive vehicles, you only need to check vehicles from the following manufacturers (as listed on the www.vehiclerecallsafety.nzta.govt.nz/takata/takataalpha):
- BMW
- Daihatsu
- Honda
- Isuzu
- Lexus
- Mazda
- Mitsubishi
- Nissan
- Subaru
- Toyota.
Vehicles from other manufacturers will not have Takata Alpha type airbags fitted, or be Japanese vehicles of concern, so are not subject to the recall.
For left-hand drive vehicles it is up to the importer to supply conclusive evidence that there is no recall for the vehicle and/or that the airbag has been replaced.
Conclusive evidence
To meet the burden of proof of conclusive evidence, it must be shown that the vehicle is not on any current recall lists generated by the manufacturer. Alternatively, where available a current list maintained by a jurisdictional authority can be used.
Also note, Japanese Shaken issued after 1 May 2018 is de facto evidence from a jurisdictional authority. The rationale for this is that 1 May 2018 is the deadline for all 'vehicles of concern' to have their mandatory recall cleared. Any Shaken issued after this date will require this recall to be closed.
Recall completion certificate
A Japanese Ministry of Land, Infrastructure, Transport and Tourism (MLIT) process document like the image below can be used to provide evidence of a Shaken test (Japanese WoF). A vehicle can only pass a Shaken test if it has had its Takata Aplha airbags replaced.
If a copy of this document is presented in for the vehicle in question and with a dealers stamp on it, it can be accepted as evidence that the vehicle in question can pass a Shaken test and therefore has had its airbags replaced. It can be accepted as proof that a vehicle has been rectified at a dealership level but might not yet have come off their website.
Example of recall completion certificate (without dealer stamp).
Other safety recalls
As the Transport Agency (or other delegated entity) makes information on additional recalls available, this process can be expanded to include those recalls for which information is available.
Page added 16 May 2018 (see amendment details)
Page updates: 31 May 2018, 8 June 2018; 26 September 2018
2 Takata non-alpha airbag recall
Following the compulsory Takata alpha airbag inflator recall order 2018 which came into effect on 31 May 2018, the Transport Agency is taking action to prohibit vehicles with any outstanding Takata airbag recalls from entering the New Zealand fleet.
The purpose of this technical bulletin is to outline, for Border Inspectors, the process for flagging vehicles subject to a Takata non-alpha airbag recalls and how to deal with them.
The process outlined below are the steps BIOs can take to assure they act with due diligence, best endeavors, and based upon the best information available.
Border Inspection Organisations
The Border Inspection Organisations, specifically Automotive Technologies Limited, ATJ, JEVIC, Independent Verification Systems (IVS), and NZ Biosecurity Services, as per the requirements of the Boarder Inspection VIRM, will provide data to the Transport Agency regarding open safety recalls on vehicles they inspect subject to the prerequisites below.
All reasonable efforts outlined in this process will be made to assure they provide the most accurate information. All responsibility for importing any vehicle remains with the importer.
The process
From 1 November 2018, Border Inspection Organisations are required to identify and report on vehicles they inspect (fitted with airbags) that are on the Takata airbag recall lists from the various source countries.
On finding a vehicle subject to recall for Takata airbag the vehicle is to be damage flagged with note added stating ‘Open Airbag Recall’.
Recalled Takata airbag vehicles from Japan
In Japan, vehicles subject to recalls are listed on the Japanese Ministry of Land, Infrastructure, Transport and Tourism (MLIT) web site at the following address, Border Inspection Organisations are to check whether the recalls have been closed in Japan, if it has been closed no action needs to be taken: https://www.jaspa.or.jp/portals/recallsearch/index
Recalled Takata airbag vehicles from other countries
Vehicles from countries other than Japan will have to be checked against official sites in those countries. These include, but are not limited to:
- USA
https://www.nhtsa.gov/recalls - Australia
https://www.productsafety.gov.au/recalls/compulsory-takata-airbag-recall/takata-airbag-recalls-list - UK
https://www.dft.gov.uk/vosa/apps/recalls/default.asp - There may be appropriate lists in other jurisdictions.
It is important to understand that this is not a new requirement it is just enforcing the existing requirement that recalls are to be closed prior to a vehicle being imported into New Zealand.
If the vehicle is on one of the lists and conclusive evidence from the manufacturer or jurisdictional authority that the airbag recall has been completed is not available, the vehicles will be damage flagged with notes recorded stating ‘Open Airbag Recall’.
Entry certification
At entry certification if a vehicle is presented with a damage flag and notes stating ‘Open Airbag Recall’ it is not to be passed until evidence is provided from the NZ manufacturer's agent that the effected airbags have been replaced.
Process flowcharts
2018年11月1日からのタカタ製エアバッグリコール対象の中古車両のボーダーインスペクションプロセス(日本から輸入車に限る)
Page added 26 September 2018 (see amendment details)
3 Vehicles fitted with ITS Connect
If any vehicle that is effected by this technical bulletin (by make/model/model code) has damage that requires photos are uploaded to BIS, please prioritise the damage photos and note the ITS-Connect status in the Damage notes. For example:
|
The ITS Connect system fitted to some vehicles originating in Japan operates by broadcasting a signal on the 760MHz frequency. This frequency is not compatible with the licensing framework in New Zealand. Under the Radio Communications Act 1989 it is illegal to import or operate a device that operates on this frequency
The purpose of this technical bulletin is to define a process for identifying vehicles fitted with ITS Connect systems and how these vehicles need to be processed if an ITS Connect system is fitted.
The process outlined below shows the steps border inspection organisations (BIOs) can take to assure they act with due diligence, best endeavours, and based upon the best information available.
BIOs to provide data to Waka Kotahi
The BIOs, specifically Automotive Technologies Limited, ATJ, JEVIC, Independent Verification Systems (IVS), and NZ Biosecurity Services, as per the requirements of this manual, will provide data to Waka Kotahi NZ Transport Agency regarding the presence of ITS Connect on vehicles they inspect, subject to the prerequisites below.
All reasonable efforts outlined in this process will be made to assure the BIOs provide the most accurate information. All responsibility for importing any vehicle remains with the importer.
The process for BIOs to follow
From 1 April 2021 BIOs must check if vehicles they inspect (that are on the defined make and model list) are fitted with an ITS Connect system.
Vehicles coming to New Zealand from Japan
Process for ITS Connect fitted vehicle
Vehicles that must be inspected for ITS Connect
Make | Model | Year | Model code |
---|---|---|---|
Lexus | ES300h | 10/2018+ | 6AA-AXZH10 |
08/2020+ | 6AA-AXZH11 | ||
Lexus | LBX | 11/2023+ | 6AA-MAYH10 6AA-MAYH15 |
Lexus | LC500 | 06/2023+ | 5BA-URZ100 |
LC500 convertible | 06/2023+ | 5BA-URZ100 | |
LC500h | 06/2023+ | 6AA-GWZ100 | |
Lexus | LS500 | 10/2017+ | DBA-VXFA50 DBA-VXFA55 |
11/2020+ | 3BA-VXFA50 3BA-VXFA55 | ||
LS500h | 10/2017+ | DAA-GVF50 DAA-GVF55 | |
10/2019+ | 6AA-GVF50 6AA-GVF55 | ||
Lexus | LX600 | 01/2022+ | 3BA-VJA301W |
Lexus | NX300 | 08/2018+ | DBA-AGZ10 DBA-AGZ15 |
07/2020+ | 3BA-AGZ10 3BA-AGZ15 | ||
NX250 | 10/2021+ | 5BA-AAZA20 5BA-AAZA25 | |
NX350 | 10/2021+ | 5BA-TAZA25 | |
NX300h | 08/2018+ | DAA-AYZ10 DAA-AYZ15 6AA-AYZ10 6AA-AYZ15 | |
NX350h | 10/2021+ | 6AA-AAZH20 6AA-AAZH25 | |
NX450h+ | 10/2021+ | 6LA-AAZH26 | |
Lexus | RX200t/RX300 | 10/2015+ | DBA-AGL20W DBA-AGL25W |
RX300 | 07/2020+ | 3BA-AGL20W 3BA-AGL25W | |
RX350 | 11/2022+ | 5BA-TALA10 5BA-TALA15 | |
RX450h | 10/2015+ | DAA-GYL20W DAA-GYL25W | |
07/2020+ | 6AA-GYL20W 6AA-GYL25W | ||
RX450hL | 12/2017+ | DAA-GYL26W | |
07/2020+ | 6AA-GYL26W | ||
RX500h | 11/2022+ | 5AA-TALH17 | |
RX350h | 07/2023+ | 6AA-AALH10 6AA-AALH15 | |
RX450h+ | 11/2022+ | 6LA-AALH16 | |
Lexus | RZ300e | 11/2023+ | ZAA-XEBM10 |
RZ450e | 03/2023+ | ZAA-XEBM15 | |
Lexus | UX200 | 11/2018+ | 6BA-MZAA10 |
UX250h | 11/2018+ | 6AA-MZAH10 6AA-MZAH15 | |
UX300e | 10/2020+ | ZAA-KMA10 | |
UX300h | 01/2024+ | 6AA-MZAH16 | |
Toyota | Alphard | 01/2018+ | DBA-AGH30W DBA-AGH35W DBA-GGH30W DBA-GGH35W |
01/2020+ | 3BA-AGH30W 3BA-AGH35W 3BA-GGH30W 3BA-GGH35W | ||
06/2023+ | 3BA-AGH40W 3BA-AGH45W | ||
Alphard Hybrid | 01/2018+ | DAA-AYH30W | |
01/2020+ | 6AA-AYH30W | ||
06/2023+ | 6AA-AAHH40W 6AA-AAHH45W | ||
Toyota | Camry | 08/2018+ | DAA-AXVH70* |
08/2020+ | 6AA-AXVH70* | ||
10/2019+ | 6AA-AXVH75* | ||
Toyota | Century | 09/2023+ | 6LA-GRG75 |
Toyota | C-HR | 05/2018+ | DBA-NGX10* DBA-NGX50* 3BA-NGX10* 3BA-NGX50* DAA-ZYX10* 6AA-ZYX11 N/A |
Toyota | Corolla Sport | 06/2018+ | 3BA-NRE210H* 3BA-NRE214H* |
06/2020+ | 6AA-ZWE211H* 6AA-ZWE213H* | ||
10/2022+ | 6AA-ZWE219H N/A 6BA-MZEA12H N/A | ||
Toyota | Crown | 08/2016+ | DBA-ARS210 DBA-GRS210 DBA-GRS211 DBA-GRS214 |
06/2018+ | 3BA-ARS220 | ||
Crown FCEV | 11/2023+ | ZBA-KZSM30 | |
Crown Hybrid | 10/2015+ | DAA-AWS210 DAA-AWS211 | |
06/2018+ | 6AA-AZSH20 6AA-AZSH21 6AA-GWS224 | ||
11/2023+ | 6AA-AZSH32 | ||
Crown Majesta | 09/2015+ | DAA-AWS215 DAA-GWS214 | |
Crown Crossover | 07/2022+ | 5AA-TZSH35 6AA-AZSH35 | |
Crown Sport | 10/2023+ | 6AA-AZSH36W | |
Crown Sport HEV | 12/2023+ | 6LA-AZSH37W | |
Toyota | Esquire | 07/2017+ | DBA-ZRR80G* DBA-ZRR85G* |
04/2020+ | 3BA-ZRR80G* 3BA-ZRR85G* | ||
Esquire Hybrid | 07/2017+ | DAA-ZWR80G* | |
04/2020+ | 6AA-ZWR80G* | ||
Toyota | Harrier | 06/2017+ | DBA-ZSU60W* DBA-ZSU65W* DBA-ASU60W* DBA-ASU65W* |
06/2020+ | 6BA-MXUA80 6BA-MXUA85 | ||
Harrier Hybrid | 06/2017+ | DAA-AVU65W* | |
06/2020+ | 6AA-AXUH80 6AA-AXUH85 | ||
Harrier PHEV | 09/2022+ | 6LA-AXUP85 N/A | |
Toyota | Land Cruiser | 08/2021+ | 3BA-VJA300W 3DA-FJA300W |
Toyota | Mirai | 12/2020+ | ZBA-JPD20 |
Toyota | Noah | 07/2017+ | DBA-ZRR80G* DBA-ZRR80W* DBA-ZRR85G* DBA-ZRR85W* |
04/2020+ | 3BA-ZRR80G* 3BA-ZRR80W* 3BA-ZRR85G* 3BA-ZRR85W* | ||
01/2022+ | 6BA-MZRA90W 6BA-MZRA95W | ||
Noah Hybrid | 07/2017+ | DAA-ZWR80G* DAA-ZWR80W* | |
04/2020+ | 6AA-ZWR80G* 6AA-ZWR80W* | ||
01/2022+ | 6AA-ZWR90W 6AA-ZWR95W | ||
Toyota | Prius | 12/2015+ | DAA-ZVW50 DAA-ZVW51 DAA-ZVW55 |
07/2020+ | 6AA-ZVW51 6AA-ZVW55 | ||
01/2023+ | 6AA-MXWH60 6AA-MXWH65 6AA-ZVW60 6AA-ZVW65 | ||
Prius PHV | 10/2016+ | DLA-ZVW52 | |
07/2020+ | 6LA-ZVW52 | ||
03/2023+ | 6LA-MXWH61 | ||
Toyota | Vellfire | 01/2018+ | DBA-AGH30W DBA-AGH35W DBA-GGH30W DBA-GGH35W |
01/2020+ | 3BA-AGH30W 3BA-AGH35W 3BA-GGH30W 3BA-GGH35W | ||
06/2023+ | 5BA-TAHA40W 5BA-TAHA45W | ||
Vellfire Hybrid | 01/2018+ | DAA-AYH30W | |
01/2020+ | 6AA-AYH30W | ||
06/2023+ | 6AA-AAHH40W 6AA-AAHH45W | ||
Toyota | Voxy | 07/2017+ | DBA-ZRR80G* DBA-ZRR80W* DBA-ZRR85G* DBA-ZRR85W* |
04/2020+ | 3BA-ZRR80G* 3BA-ZRR80W* 3BA-ZRR85G* 3BA-ZRR85W* | ||
01/2022+ | 6BA-MZRA90W 6BA-MZRA95W | ||
Voxy Hybrid | 04/2020+ | DAA-ZWR80W* 6AA-ZWR80W* | |
01/2022+ | 6AA-ZWR90W 6AA-ZWR95W |
* indicates ITS is a dealer's option for this model.
Inspecting the vehicle for an active ITS Connect system
To determine if ITS Connect is fitted and operational, two checks must be made to the vehicle. The first check is on the driver information display (MID, or MFD). The second check is on the navigation system.
In both cases the inspector will be looking for any indication of settings that are associated with an active ITS Connect system.
Note: the images below do not cover all vehicles. This page will be updated as manufacturers supply further content and advice. |
ITS Connect manufacturer option inspection
ITS Connect dealer option check
Identifying ITS Connect in a Toyota Prius
Video example
Visual guide to identifying ITS Connect in a Toyota Prius
Figure 1. Settings selector button
Figure 2. Setting screens
Use arrows on steering wheel control pad to move the selector
Figure 3. ITS Connect fitted as shown under vehicle settings
This vehicle would need to be damaged flagged and have the system removed.
Identifying ITS Connect in a Toyota Vellfire
Video example
Visual guide to identifying ITS Connect in a Toyota Vellfire
Figure 4. Vellfire MFD control buttons
Figure 5. Vellfire MFD
Figure 6. Scroll Right to find settings
Figure 7. Select the gear icon for settings
Figure 8. Scroll down and select 'Vehicle Settings'
Figure 9. Scroll down
If ITS connect is fitted you will see the settings as below.
Conclusive evidence of inspection and ITS Connect system removal
To meet the burden of proof of conclusive evidence, it must be shown that the vehicle is not fitted with an ITS Connect system.
For a vehicle that is not fitted with ITS-Connect two photos must be saved to the BIO's vehicle file that show the settings screens for both the Navigation unit and the MID. The vehicle's damage notes (in the vehicle's file) must be updated to show that the vehicle has been inspected for ITS-Connect and ITS-Connect is not fitted, eg 'ITS-Connect not identified'. Note: damage notes cannot be added to BIS as the vehicle does not need a damage flag applied.
For a vehicle that is not fitted with the system, two photos must be provided on the BIS system that show the settings screens for both the Navigation unit and the MID. These photos should also be saved with the BIO’s vehicle file. These can be loaded manually without applying a damage flag.
A vehicle that has been found to be fitted with an ITS Connect system must have a damage flag placed on the vehicle with a note stating ‘ITS Connect Fitted’. Any other damage or Takata airbag recall notes must also be added if applicable. The damage flag is to remain on the vehicle even if ITS-Connect is disabled in Japan. Note: The vehicle record should not be created on BIS until the vehicle has completed its final border inspection, once a damage flag has been placed the record cannot be edited.
The vehicle owner must take the vehicle to a Toyota or Lexus franchise in Japan to have the ITS Connect system removed. An invoice or receipt from the dealer that shows the vehicles chassis number and indicates that the system has been removed is acceptable evidence that ITS Connect is no longer fitted.
After the ITS-connect is disabled a secondary check must be made on both the Navigation unit settings and the MID settings to ensure the ITS Connect associated settings are no longer visible. A copy of the invoice and photos of the displays on the second inspection must be saved in the vehicle file. A copy of the invoice should be loaded to BIS as evidence of the ITS Connect system removal. The invoice should be uploaded as a photo. PDFs cannot be uploaded unless the vehicle is water damaged. The vehicle should not be recorded as water damaged for the purpose of ITS Connect.
Page amended 4 March 2024 (see amendment details)
4 Acid wash process on used imports
Vehicle inspection requirements manuals reference:
Reference materials
1 Guidelines for the detection of reportable damage on imported used vehicles (excl motorcycles)
Vehicles imported from Australia Every vehicle imported from Australia will need to have a Personal Property Securities Register (PPSR) certificate downloaded from https://transact.ppsr.gov.au/ppsr/SearchForMotorVehicle?v=Search If the certificate identifies the vehicle as 'written off' it must be reported as damaged and a copy of the PPSR certificate uploaded into the Border Inspection system. |
1 Introduction
This guide is designed to provide foundation material to assist vehicle inspectors in the requirements for inspecting imported used motor vehicles; and the identification, recording, and flagging of structural damage.
The use of diagrams and photographs is used to support the written standards listed in the guide and illustrates:
- structural areas of unibody and body-over-frame vehicles
- energy management paths
- examples of the types of structural damage that needs to be reported.
Note: Refer to Reference material 10 for guidance on the inspection of motorcycles. |
Vehicle fitted with ITS Connect
A vehicle must be reported if there is evidence that the ITS Connect system is fitted to the vehicle. The damage flag is to remain on the vehicle even if the ITS Connect system is disabled in Japan.
Note: Refer to Technical bulletins 3 Vehicles fitted with ITS Connect
Option - (excluding MD1, MD2 minibus)Vehicle not fitted with Electronic Stability ControlA vehicle must be reported if there is evidence that an electronic stability control (ESC) system is NOT fitted to the used motor vehicle of class MA, MB, MC, or NA. This provision will not apply to a vehicle manufactured, or first registered outside of New Zealand, 20 years or more at the time of the border inspection. Notes
|
2 Purpose
The purpose of the guide is to provide vehicle inspectors with reference material stipulating the standards for reportable structural damage, supporting information, and to assist in the decision-making process when an imported used vehicle must be reported to Waka Kotahi (or ‘flagged’).
Exclusions to flagging of structural parts, ie those that do not require reporting are described and explained.
This guide also gives examples of ‘minor’ damage, which would be considered as cosmetic, and do not require reporting to Waka Kotahi.
3 Overview – Structural parts: Unibody chassis
1 Inner guard | 8 Cant rail | 15 Rear seat floor | 22 Front bumper |
2 Upper chassis rail (reinforcer) | 9 Roof (not shown) | 16 B pillar | 23 Spare wheel well |
3 Strut tower | 10 C pillar (upper) | 17 Floor | 24 Tunnel (longitudinal) |
4 A pillar (upper) | 11 Rear panel | 18 Sill (rocker panel) | 25 Rear seat cross beam |
5 Windscreen header | 12 Rear ¼ panel | 19 A pillar (lower) | 26 Rear suspension cross beam |
6 Roof stiffener | 13 Boot floor | 20 Bulkhead | |
7 Parcel tray | 14 Rear seat back | 21 Lower (engine) chassis rail |
4 Overview – Structural parts: Body-over-frame chassis
5 Overview – Energy management path
The structural integrity of the passenger safety cell is a key feature of motor-vehicle design.
- Front and rear structural parts are designed to absorb or manage collision energy by collapsing in pre-determined areas called crush zones.
- Crush zones are built into the front and rear of the vehicle in the form of holes, slots, dimples, convolutions, or hydro-formed tailored blanks.
- Bonnets are designed to buckle and avoid windscreen penetration, and also minimise pedestrian injury.
- The unibody structure is designed to route collision energy around the passengers; with the passenger safety cell the last area to deform in a crash where collision energy exceeds the design.
6 Criteria for reporting structural damage or corrosion
The following information gives guidance to vehicle inspectors in determining whether or not a light vehicle (including motorcycles where applicable) undergoing border inspection requires reporting.
Applicable legislation
Vehicles to which this section applies must be inspected by a vehicle inspector or inspecting organisation appointed under 2.2(1)(k) in accordance with requirements and conditions imposed by Waka Kotahi under 2.3.
The criteria detailed below must be used when deciding if any damage or corrosion should be reported. All damage meeting this criteria and found in the energy management path areas must be reported.
The important distinction when applying these criteria is:
- Whether the area identified as damaged by impact, previous repair, or corrosion is structural or cosmetic, and
- Whether the extent of damage is sufficient to compromise the structural integrity of the motor vehicle, or
- Whether evidence of damage, previous damage repair, or heat damage is present in a structural area, or energy management path of the motor vehicle.
Photographs illustrating examples of structural damage and corrosion are shown in Reference material 5.
Under-body impact damage
A vehicle must be reported if it has underbody damage as a result of a collision with a substantial object, sufficient to cause the splitting of seam welds, distortion of suspension members or mounting points, or tearing of metal structures, excluding floorpan stiffeners (Note 1).
Note 1
When distinguishing between floorpan stiffening members and cross-members, note that a member that runs through the line of a seat or occupant area will not be an energy absorbing member (ie its purpose is to reinforce the floorpan), while a member that runs alongside a seat or occupant area should be treated as an energy absorbing member (ie a chassis rail).
Denting or distortion
- A vehicle must be reported if there is any discernible denting or distortion to the folds or swages in the dog leg, sill panel or structure of the inner/outer sill weld seam, other than minor scraping.
- A vehicle must be reported if rocker panels (outer sills) are dented or creased lengthways along the sill and the depth of the crease exceeds 25mm.
- A vehicle must be reported if rocker panels (outer sills) are vertically dented or creased across the sill regardless of the depth of the crease or dent.
Outer sills cross section and rocker panels
Crush zones and kick-up areas
A vehicle must be reported if there is distortion of the longitudinal rails affecting the front and rear crush zones and kick-up areas.
Crossmembers
A vehicle must be reported if there is denting or distortion of the crossmember as a result of collision with an object.
Cracking
A vehicle must be reported if there is cracking in:
- the unibody chassis
- any crossmembers and subframes
- a load bearing member, or energy management paths in unibody structures
- the body of a vehicle with a body-over-frame chassis in the energy management paths, engine mounts, suspension mounts, body mounts, pillars, or sills.
Repaired damage
A vehicle must be reported if signs of fresh repair, rust prevention, acid wash (see Technical bulletin 4: Acid wash process on used imports) or under-sealing to any part of the vehicle structure are evident.
Supplementary Restraint System (SRS): Airbags and seatbelt pretensioners
A vehicle must be reported if it has a deployed airbag or seatbelt pretensioner, or there is evidence of repairs to or tampering with airbag module covers. (including colour variations in plastic covers to steering wheels, dash panels, interior trim, or non-original stitching to seat mounted airbags). A vehicle must be reported if the SRS warning light stays illuminated when the engine is running.
Water damage, fire damage or other written off vehicles
A vehicle must be reported if there is evidence that it has suffered water damage, fire damage or the veicle has been written off (Note 2).
Note 2
For the purposes of the border inspection, evidence of water or fire damage may be physical evidence, or it may be that the vehicle has been written-off for insurance purposes as a result of water, fire >or other damage.
Corrosion Damage
- Corrosion damage is where the metal has been eaten away, which is evident by pitting. The outward signs of such corrosion damage are typically displayed by the swelling of a panel between spot welds, or lifting or bubbling of paint. In extreme cases, the area affected by the corrosion damage will fall out and leave a hole.
A vehicle must be reported if there is corrosion damage in any structural area, as indicated in the shaded areas of Figure 1-1-1.
Note 4
For the purposes of the border inspection, corrosion damage includes any signs of ‘rust bleed’. Rust bleed is a rust coloured stain or mark that appears around an area of corrosion that may not be visible. Rust bleed is most commonly found where panels join or overlap when corrosion has started between the two surfaces and moisture has caused a rust stain or mark to run onto the external surface.
- Perforated corrosion is where the metal is corroded to the extent that it has holes, or holes are exposed when rust scale is removed. If metal is badly pitted causing a loss of metal thickness it must also be treated as perforated corrosion.
If there is perforated corrosion in any other (non-structural) area, as indicated in the non-shaded areas of Figure 1-1-1, the vehicle requires to be reported.
Figure 1-1-1. Structural corrosion damage limits
Corrosion, or the repair of corrosion on ‘bolt on’ parts (doors, bonnets, and boot lids)
within a 150mmcircle around the outside of hinge or latch components will require to
be reported. These ‘no corrosion’ zones are circled in Figure 1-1-2.
Figure 1-1-2. Hinge and latch anchorage corrosion damage limits
7 Cosmetic damage
Cosmetic damage to the motor vehicle’s outer body panels is permitted, providing it does not affect the structural integrity of chassis, the energy management paths, or any of the bonded or welded seams or joints as a result of the manufacturing process.
Cosmetic parts on a unibody chassis are generally bolt on items such as the front guard, boot-lid, and in most cases the doors.
Photographs illustrating examples of cosmetic damage are shown in Reference material 6.
Inspection
A list of specific types of damage follows. It explains the extent to which damage is allowed before a vehicle must be reported.
Underbody impact damage
- A vehicle does not require reporting if it has minor underbody impact damage as a result of ‘grounding’ the vehicle or some scraping of the sill seams.
- A vehicle does not require reporting if there is crushing or tearing of floorpan stiffening members (Note 5), provided it does not affect any internal cross-members designed for side-impact protection.
Note 5
When distinguishing between floorpan stiffening members and cross-members, note that a member that runs through the line of a seat or occupant area will not be an energy absorbing member (ie its purpose is to reinforce the floorpan), while a member that runs alongside a seat or occupant area should be treated as an energy absorbing member (ie a chassis rail).
Denting or distortion
A vehicle does not require reporting if rocker panels (outer sills) are dented or creased lengthways along the sill to a depth of less than 25mm.
Cross-members
A vehicle does not require reporting if it has minor jacking damage to a cross-member, provided there is no indication of loss of steering or suspension alignment.
Repaired damage
A vehicle with repaired damage does not require reporting if repairs are only to correct cosmetic damage to the outer body panels, provided the vehicle inspector is able to discern the extent of the damage and confirm that none of the vehicle manufacturer’s seams or joints have been disturbed during the repair.
Entry vehicles with known corrosion problems
Mitsubishi
Diamante:Floor/front strut towers
Legnum: Under body/Strut towers
Lancer Evo: Rear rails
Delica van: Front rails
Nissan
Safari: Floor/front and rear cross members/radiator support panels
Terrano: Floor area
Mistral: Floor area
Pulsar: Under body and inner floor/sill joint
Mazda
Demio: Front cross member
MPV: Rear chassis rail
8 Ancillary Procedures
Doubt regarding damage status
If after completing the check on the vehicle there is any doubt whether to report the damage found, the following approach should be applied.
IF IN DOUBT DO NOT REPORT THE DAMAGE
Exceptions to flagging of structural parts
The front windscreen and all other glass is a structural part in the Unibody chassis, and modern (light) Body-over-frame chassis. For the purpose of entry-level inspection, the glass is not to be flagged as a damaged structural item, unless the cause of the windscreen damage can be attributed to airbag deployment or other structural damage that must also be flagged.
Page amended 1 October 2023 (see amendment details)
2 Border inspection system guidelines
2-1 System guidelines overview
Border inspection system
The purpose of the border inspection system is to record the data collected by service providers when border inspections are performed on used vehicles intended to be imported into New Zealand.
Entering border inspection records
Border inspection records can be entered individually through a user interface, or stored in a batch file and uploaded to the system via the border inspection system homepage.
A border inspection record must be entered within 48 hours of the inspection being carried out for vehicles inspected in New Zealand and within five days after the ship has departed for vehicles inspected offshore.
Access to methods of entering records
Access to both methods of entering a record is via the homepage of the border inspection system website.
Duplicate records will not be accepted.
Note: To increase the font size in the system, select and hold Control (Ctrl) whilst simultaneously rolling the scroll wheel on your mouse.
Logging into the system
Refer to the Accessing and logging into the system section for instructions on how to access the NZTA online services and log in to the border inspection system.
Border inspection system homepage
Attachments
Border inspection records may include attachments; attachments may be a combination of images and one water damage report. Refer to the Attachments section for further information about attachments and their specifications.
Contact details
To access NZTA contact details, hover your mouse over Contact Us at the top right-hand side of the screen. The message will refer you to the VIRM, page 2-1 for the relevant NZTA contact details.
2-2 Accessing and logging into the system
Logging into the border inspection system
Step | Action |
---|---|
1 | Open a new browser window and enter the following URL: https://accessportal.nzta.govt.nz/ Please note: the portal does not support Internet Explorer, please use a different browser, |
2 | This will provide access to the Waka Kotahi online services access point: |
3a | To access the system for the first time you must accept an invitation. Select the Use invitation code button. This will take you to the Redeem invitation code screen. Enter invitation code and select Continue. You will be directed to the Realme login page – go to step 4. Note: You only need to accept an invitation once, to register to the portal. For all subsequent logins go to step 3b. |
3b | To login, select Login via realme. |
4 | You will be directed to the Realme login page. Enter your realme login. |
5 | Successful login will direct you to the Access portal home page. Your home page will be either the General user home page or the Organisation administrator home page. General user home pageOrganisation administrator home page |
6 | Select Go to your online applications. |
7 | This will take you to the Access online applications screen. Select the green Access application button next to Border inspection system (BIS). |
8 | You will be directed to the Border inspection system home page. |
9 | Unsuccessful login screen. |
Page amended 8 November 2022 (see amendment details)
2-3 Border Inspection System administration and corrections information
The following information is to assist Border Inspection Organisations (BIOs) new to the Border Inspection System (BIS). It provides quick administrative answers to some frequently asked questions.
BIS system
A batch file is accepted into BIS excluding any errored records. Errored record should be corrected and sent in a new batch file.
- The same batch file will not be accepted twice, and the system does not accept duplicate records.
Occasionally you may have a second border inspection for the same vehicle or another vehicle using the same chassis number. For authority to load the record using an alternative chassis field, email borderchecks@nzta.govt.nz providing the error message and the border inspection details for review. An alternative solution may be provided.
If copying and pasting data into a record, please ensure low value characters (usually @ * ^ ~) are not included.
There are two uploads from BIS to LANDATA each day.
- Records received prior to 1:00am (NZ time) are uploaded to LANDATA at 6:00am (NZ time).
- Records received prior to 1:00pm (NZ time) are uploaded to LANDATA at 2:00pm (NZ time).
Photos
Four photos can be loaded with the border inspection record. An additional four can be added to an existing record. If there are photos, keep them with your records as we can ask if they’re needed.
For more information see 2-8 Adding additional images to an existing record
Updated NZTABusinessDataTypes.xsd files are emailed when the Motor Vehicle Register (MVR)/LANDATA system tables have been updated. These files are provided to ensure that the information you load will be accepted into BIS and will also load into LANDATA. For example, a border inspection record loaded into BIS using an invalid make will load into BIS but not LANDATA. For example, Mercedes-Benz is correct but M/Benz and Mercedes Benz are invalid.
Included in the file are:
- ISO list of three-character country codes
- list of Ports
- list of border inspection sites
- makes
Correcting errors to border inspection records
Inspection dates, importer names, ship names, or port of arrival
Send a copy of the border inspection checksheet to borderchecks@nzta.govt.nz and we will update the LANDATA record.
VIN/chassis number recorded incorrectly
Advise the incorrect number to your customer.
Your customer (or the importer/owner) should provide the incorrect VIN or chassis number to a New Zealand entry certification agent. The entry certifier will verify the correct VIN or chassis number physically on the vehicle. If it’s a chassis number, the agent can correct it. If it’s a factory VIN and both the incorrect and correct VINs are valid in LANDATA the entry certification agent will contact Waka Kotahi NZ to fix.
Make and/or Model
This will be corrected by the entry certifier. They will inspect the vehicle and ensure the vehicle attributes that have been loaded into LANDATA are correct.
Damage flag set in error
Send an explanation to borderchecks@nzta.govt.nz and if appropriate we will remove the damage flag in LANDATA.
Damage flag not set
Send the damage notes and photos to borderchecks@nzta.govt.nz. The damage flag and damage note will be added to the LANDATA record. The photos (up to eight) will be added to the BIS record. If there are numerous records requiring correction, an alternate process may be given.
Incorrect Odometer reading
Email a photo of the odometer reading taken during border inspection and/or a copy of any paper-based documentation that shows the actual odometer reading recorded by the inspector to borderchecks@nzta.govt.nz
If your documentation shows the recorded odometer reading and the customer (or the importer/owner) believes the odometer reading it’s incorrect, they or their NZ entry certification agent should email the following to frr@nzta.govt.nz for consideration:
- A copy of the entry certification checksheet, and
- Other official inspection documents (shipping and auction/sales documents are not appropriate) showing the odometer reading in the previous country of registration, or
- Documentation from a recognised NZ odometer specialist certifying that the odometer has not been tampered with and it’s considered to correctly record the distance the vehicle has travelled at the time of inspection.
Where keying error can't be identified
Where a keying error cannot be verified, the public display of odometer records can be suppressed. This is discretionary and based on risk and supporting documentation. If the information provided is not deemed sufficient, we will not change the odometer reading leaving it publicly available to allow the public to come to their own decision as to the vehicle's correct mileage.
Any other questions concerning the Border Inspection System (BIS) and the Motor Vehicle Register System (LANDATA), please email borderchecks@nzta.govt.nz
Page added 1 October 2022 (see amendment details)
2-4 Entering an individual record
Creating a new record
Step | Action |
---|---|
1 | On the homepage, create a new record by using one of the methods below:
|
2 | A new window will open and display the following form: |
3 | Complete the necessary fields. Note: Refer to the Completing the form section for additional information about entering details. |
4 | When all fields have been completed and all attachments (if necessary) have been added, to save the record, click on OK. |
2-5 Completing the form
Standard mandatory fields
In the Create New Record screen, any field that is preceded by an * is a mandatory field and must be populated before the record is submitted.
The following fields are mandatory:
- Identifier
- Make: select from a drop-down list
- Model: free text
- Inspector ID: free text
- Inspection Date: select using the calendar picker
- Left Hand Drive: automatically defaults to ‘No’
- Border Odometer: must contain a value greater than, or equal to, zero
- Site: select from a drop-down list
- Importers Name: free text
- Importers Address: free text
- Ship Name: free text
- Port of Arrival: select from a drop-down list
- Country of Import: select from a drop-down list
- Damage: automatically defaults to ‘No’.
Additional notes for vehicle section
- Identifier: at least one identifier must be entered for a record. Either:
- VIN ISO, or
- Other VIN
Do not enter a vehicle identifier into the ‘Chassis’ field.
- Make: if you select Other in the Make drop-down list, enter the make details for the record in the Other Make box.
Note 1
VIN ISO:
- cannot include: ‘O’ for Oscar, ‘I’ for India or ‘Q’ for Quebec
- must be 17 characters in length
- must not have a dash (-) entered in the number.
Note 2
A Japanese domestic VIN will always have a dash (-) somewhere in the VIN.
Additional notes for inspection section
- Inspector ID: Use the person’s initials followed by a sequential number which identifies the inspector.
- Inspection date: the inspection date must be entered as yyyy/mm/dd. Select a date by using the date picker icon to the right of the Inspection Date box.
Note: The date cannot be in the future. - Border Odometer: border odometer readings must be values that are equal to or greater than zero. If no odometer reading can be recorded, enter ‘00000’
- Site: if you select Other in the Site drop-down list, enter the site details for the record in the Other Site box.
- Ship name: If you want to record the voyage number, use this field following the name of the ship, eg Transfuture 6 (VOY 48)
- Port of Arrival: if you select Other in the Port of Arrival drop-down list, enter the port details for the record in the Details of Other Port box.
- Country of import: this is the country that the vehicle was exported from.
- Damage: if the No button is selected, the Damage section will not appear and no further fields need to be completed. If the Yes button is selected, further fields related to damage will appear enabling notes, photos and/or water damage reports to be attached to the record. Refer to the Entering further information if the vehicle is damaged section for further details.
2-6 Entering further information if the vehicle is damaged
Create new record screen with additional damage fields
Mandatory fields for damage information
If the vehicle has been damaged, the following fields are mandatory:
- Damage
- Structure Damage
- SRS Damage
- Fire Damage
- Water Damage
- Damage Notes
- Damage Photo 1.
Additional notes for the damage fields
- Damage: if you select the Yes button, you must supply at least one photo with the record showing the damage to the vehicle. Refer to Damage Photo 1 bullet point below.
- Damage notes: when entering damage notes, select from the following list to describe the type of damage and where the damage is on the vehicle.
Damage Rust |
External Underbody Internal |
Front Rear Side |
Left Right |
Note: When a modified vehicle is flagged, record in the notes "suspect modification to the vehicle".
- Water Damage: if you select the Yes button, you must supply a water damage report with the record. Refer to Water Damage Report bullet point below.
- Damage Photo 1: click on Browse… to locate the photos to be attached.
Note: Photo pixels must not exceed 640 x 480 pixels. Minimum of two photos must be attached.
- Water Damage Report: click on Browse… to locate the file to be attached
- Refer to the Attachmentssection for detailed specifications for photographs and reports.
2-7 Entering multiple border inspection records (batch files)
Introduction
Multiple border inspection records can be loaded in an .xml file and submitted for upload to the border inspection system.
Uploading a batch file
Step | Action |
---|---|
1 | On the homepage, upload a batch file by using one of the methods below:
|
2 | A new window will open requesting that you select a file to upload: |
3 | Click on Browse… to locate the batch file stored on your system. |
4 | After you have selected the relevant file, click on OK. |
Batch file specifications
- The file must be supplied in an xml format that meets the NZ Transport Agency (NZTA) border inspection schema. For a copy of the schema, refer to the technical specifications that were supplied with your NZTA contract.
- Images and jpegs are to be incorporated as part of the inspection record and included in the xml file
- The following fields must be populated in upper case:
» UnknownMake (eg KAMAKUSA)
» ImporterName (eg FAST CARS INC)
- The following fields must be populated in title case:
» UnknownPort (eg Whanganui, not whanganui or WHANGANUI)
» UnknownSite (eg Pokeno, not pokeno or POKENO).
2-8 Adding additional images to an existing record
7 Adding additional images to an existing record
Overview
- An additional four images may be added to an existing border inspection record
- Additional images must be located, selected and then submitted for inclusion with an existing inspection record
- Additional images can only be uploaded to one inspection record at a time.
Adding additional images
Step | Action |
---|---|
1 | On the homepage, add additional images by using one of the methods below:
|
2 | A new window will open that provides browser capability to enable additional images to be selected: |
3 | Enter the Identifier associated to the existing inspection record that you wish to add the images to. This will be either:
Note: VIN ISO cannot include: ‘O’ for Oscar, ‘I’ for India or ‘Q’ for Quebec, and must be 17 characters in length. |
4 | Next to Image 1, click on Browse… to locate the image to be uploaded. Refer to the Attachments section for attachment specifications. |
5 | Once selected, the name of the image for uploading will be displayed in the Image 1 box. |
6 | Use the Image 2, 3 and 4 boxes to upload more images, if necessary, clicking on Browse… beside each box to locate the images to be uploaded. |
7 | After you have uploaded all necessary images, click on OK. |
2-9 Attachments
8 Attachments
Water damage report
When a record indicates that the vehicle has water damage, a water damage report must be included. This is stored as a jpeg file and submitted with the initial record:
- only one water damage report is permitted for inclusion with a record
- a water damage report cannot be submitted as an additional attachment after the initial record has been entered into the system.
See Reference material 4 for a copy of the water damage report form.
Technical specifications – water damage report
A water damage report jpeg must be a minimum size of 200kb and cannot exceed 400kb.
Photos
When a record indicates that the vehicle has damage, it must have at least one photo attached when the initial record is submitted:
- up to four images can be loaded with the initial record and another four images can be loaded separately for the record after the initial submission.
Technical specifications – photos
All photos supplied with records must meet the following specifications. Each image must:
- be formatted as a JPEG
- 640 x 480 pixels in size
- RGB, 24 bits per pixel
- Minimum DPI of 72, maximum of 180.
2-10 Example error messages (screenshots)
9 Example error messages (screenshots)
Error messages
When insufficient or incorrect information is entered by the user, an error message will display.
The message appears at the top of the page in red font and fields that require populating are also highlighted in red.
Example 1: Create new record
Example 2: Create new record
Example 3: Submit additional images
3 Notice to the importer
Image updated 19 April 2024
5 Examples of major structural damage and corrosion
5-1 Under-body damage: Crushing of floor pan stiffening members
The damage in these images must be referred to a repair certifier to determine whether the damage is structural or non-structural.
Where it's determined that the damage is non-structural, and there's no other damage requiring an LT308, the repair certifier will issue an LT307.
Page amended 21 February 2024 (see amendment details)
5-2 Under body damage: Splitting of seam wells
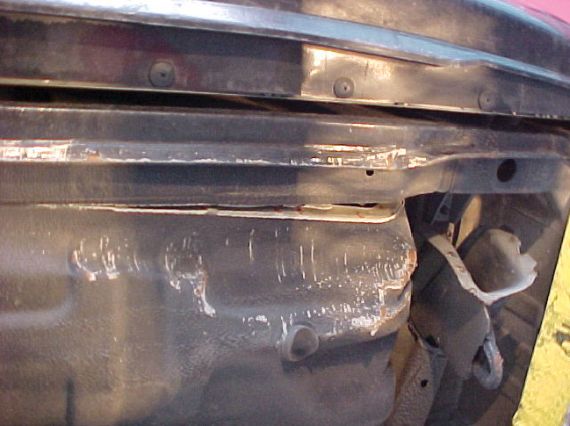
5-3 Under body damage: Tearing of the metal
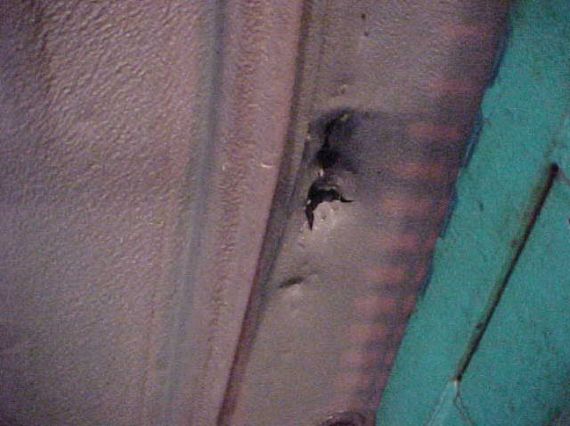
5-4 Damage to rocker panels and cant rails
Rocker panels
Cant rails
Page amended 1 October 2023 (see amendment details).
5-5 Rear quarter/dogleg
5-6 Dogleg flag
Look for discrepancies in the door gap.
5-7 Distortion to longitudinal rails: Front and rear crush zones
5-8 Collision damage to steering or suspension components
5-9 Damage to the vehicle’s outer body panels: Seam or joint integrity
Damage to the vehicle’s outer body panels which affect the integrity of any of the seams or joints installed by the vehicle manufacturer (and may have also caused secondary damage - further inspection may be required)
5-10 Corrosion which has resulted in perforation or flaking of the metal: Nissan Terrano and Mistral
When inspecting Nissan Terranos or Mistrals always check for corrosion of the floor under the rear seat (examples are shown in the first three photos below).
5-11 Water damaged vehicles
5-12 Heat and fire damaged vehicles
5-13 Examples of repairs
6 Examples of minor non-structural cosmetic damage
6-1 Front guards
6-2 Sills/rocker panels (minor damage)
6-3 Minor/cosmetic damage: Rear quarter panel and dogleg
6-4 Minor/cosmetic damage: Floor pan stiffening members
The minor/cosmetic damage in these images doesn't need to be referred to a repair certifier.
Page added 21 February 2024 (see amendment details)
7a Checksheet specifications (vehicles inspected in NZ)
Overview
The Transport Agency preference is to have one standard checksheet that is used by all border inspection service providers.
General requirements applicable to all checksheets
- The checksheet must contain an ‘Appointed by Waka Kotahi NZ Transport Agency’ logo. Please email channels@nzta.govt.nz for requirements for the use of the logo.
- The checksheet must contain the version number and/or version date of the checksheet (eg 5/09, indicating that the checksheet was last approved/changed in May 2009).
- The checksheet must include the following information:
- The words: ‘Complaints regarding border inspection issues should be first directed to the border inspection organisation’. Additional words may be added to the checksheet to meet the requirements for complaint statements contained in the Introduction section of the VIRM.
- The words ‘NZ Transport Agency reserves the right to recheck any vehicle following an inspection.’
Items to be on the checksheet
- The checksheet shall contain all the items to be recorded and checked by the vehicle inspector during a border inspection.
- Any additional items included must be relevant to the inspection requirements in the VIRM.
Items required to be recorded on all checksheets
- Inspecting Organisation name
- Address where inspection was carried out
- Vehicle Make
- Vehicle Model
- Vessel Name
- Voyage number (optional)
- Vehicle Identification Number (VIN)
- Inspection date
- Vehicle Inspector’s name
- Vehicle Inspector’s signature
- Indication of vehicle structural inspection pass or fail
- Diagram of vehicle/s
- For damaged vehicles a check list (see below) detailing type of damage and where damage is located on the vehicle
- Damage
- Rust
- External
- Under body
- Internal
- Front
- Rear
- Side
- Left
- Right
- Odometer reading
- Left-hand-drive/right-hand-drive
- Provision for notes to be recorded.
7b Checksheet specifications (vehicles inspected outside NZ)
Overview
The NZTA preference is to have one standard checksheet that is used by all border inspection service providers.
General requirements applicable to all checksheets
- The checksheet must contain an ‘Appointed by NZ Transport Agency’ logo. Please refer to the latest version of the NZ Transport Agency Visual identity guidelines via this link for requirements for the use of the logo.
- The checksheet must contain the version number and/or version date of the checksheet (eg 5/09, indicating that the checksheet was last approved/changed in May 2009).
- The checksheet must include the following information:
- The words: ‘Complaints regarding border inspection issues should be first directed to the border inspection organisation’. Additional words may be added to the checksheet to meet the requirements for complaint statements contained in the Introduction section of the VIRM.
- The words ‘NZ Transport Agency reserves the right to recheck any vehicle following an inspection.’
Items to be on the checksheet
- The checksheet shall contain all the items to be recorded and checked by the vehicle inspector during a border inspection.
- Any additional items included must be relevant to the inspection requirements in the VIRM.
Items required to be recorded on all checksheets
- Inspecting Organisation name
- Address where inspection was carried out
- Vehicle Make
- Vehicle Model
- Vehicle Identification Number (VIN)
- Inspection date
- Vehicle Inspector’s name
- Vehicle Inspector’s signature
- Indication of vehicle structural inspection pass or fail
- Diagram of vehicle/s
- For damaged vehicles a check list (see below) detailing type of damage and where damage is located on the vehicle
- Damage
- Rust
- External
- Under body
- Internal
- Front
- Rear
- Side
- Left
- Right
- Odometer reading
- Left-hand-drive/right-hand-drive
- Provision for notes to be recorded.
8 The border inspected sticker
Shown below is an example of the 'border inspected' sticker.
- Note that logos of the border inspection organisation will be in the top or bottom right corner.
Sticker image updated 18 April 2024.
9 Procedure for inspecting vehicles ... without having the NZTA border inspection
Procedure for inspecting vehicles that have been released from a Customs controlled area (CCA) or MPI transitional facility (TF) without having the Waka Kotahi border inspection
Before carrying out the Waka Kotahi border inspection the following procedures must be followed:
Verify the date when the vehicle arrived in New Zealand by sighting either a Customs clearance document or a MPI bio-security clearance certificate.
Inspect the vehicle to verify that the vehicle identification number (VIN) is the original identifier that was fitted by the vehicle manufacturer.
Carry out the Waka Kotahi border inspection and data transfer process.
Collect the Waka Kotahi border inspection fee as part of the cost of inspection.
10 Inspection of motorcycles
Vehicles imported from Australia Every vehicle imported from Australia will need to have a Personal Property Securities Register (PPSR) certificate downloaded from https://transact.ppsr.gov.au/ppsr/SearchForMotorVehicle?v=Search If the certificate identifies the vehicle as 'written off' it must be reported as damaged and a copy of the PPSR certificate uploaded into the Border Inspection system. |
When inspecting motorbikes the areas to inspect are:
The front forks, and their operation
- This is done by pushing down on the front forks of the bike and watching the fork operation
- Make sure the operation is smooth
- Make sure there is no binding felt when doing this.
Steering head area for misalignment
- Carry out a good inspection of this area, making sure the head angle is per factory and not bent, pushed back or fractured.
The motorbike frame
- Look for previous repairs as well as existing damage
- This is carried out by a good general inspection of the frame and factory welded joins and seams. You’re looking for stress markings in the weld or seam areas and or signs of previous repairs such as file marks miss matched paint or existing damage.
Figure 10-1-1. VIN number location
VIN number is found on the steering head, stamped into the metal.
Figure 10-1-2. Plastic flarings
Modern motorbikes have a lot of plastic flarings covering the frame.
It is important that the inspector check behind these flaring’s for damage.
Figure 10-1-3. Stripped down bike frame
Figure 10-1-4. Check the frame
Check frame for damage
Page amended 29 March 2023 (see amendment details)